Global Prefabrication Market Overview
Prefabrication Market Size was valued at USD 2,11,400.0 Million in 2023. The Global Prefabrication industry is projected to grow from USD 2,24,612.5 Million in 2024 to USD 3,47,846.2 Million by 2032, exhibiting a compound annual growth rate (CAGR) of 5.62% during the forecast period (2024 - 2032).
Demand for cost-effective, expedited construction methods in response to the rapid pace of urbanization and industrialization drives the demand for Prefabrication through the forecast period.

Source: Secondary Research, Primary Research, MRFR Database, and Analyst Review
Prefabrication Market Trends
-
Growing Demand for Sustainable and Energy-Efficient Building Solutions
The increased demand for sustainable and energy-efficient building solutions is a significant driver of the Prefabrication Market. This driver is significantly influencing the industry, primarily because of the increased emphasis on green construction practices and the growing awareness of environmental issues. Prefabrication is becoming a viable solution that is consistent with the environmental objectives as the global focus is heightened on the reduction of carbon emissions and the mitigation of climate change. The trend toward sustainability in construction is primarily driven by the implementation of more stringent building codes and regulations that are designed to enhance energy efficiency and minimize environmental impact. To encourage the adoption of environmentally friendly construction practices, governments and regulatory bodies worldwide are enacting increasingly stringent standards. For example, the Paris Agreement and other international agreements have encouraged numerous nations to reduce their greenhouse gas emissions. In response, a growing number of builders and developers are incorporating prefabrication into their projects, as it enables the incorporation of energy-efficient features and aligns with the changing regulations. Furthermore, the demand for prefabricated structures is further bolstered by the fact that a variety of countries are providing incentives and subsidies to encourage the adoption of sustainable construction practices. This trend is also significantly influenced by technological advancements.
The development of sustainable and energy-efficient building components is being facilitated by advancements in prefabrication technology, including modular construction and 3D printing. These technologies enhance thermal performance of buildings and reduce waste by enabling a higher degree of precision in the manufacturing process. Modern prefabricated modules, for instance, can be engineered with improved insulation and integrated renewable energy systems, resulting in reduced energy consumption and enhanced environmental performance. The market is expected to develop further as the capabilities of prefabrication to support green building practices continue to expand as technology continues to evolve.
Prefabrication Market Segment Insights
Global Prefabrication Product Type Insights
Based on the Product Type, the Prefabrication Market has been bifurcated into panels, modules, frames, girders, and others. Prefabricated panels are a critical product category in the Prefabrication Market. They are factory-manufactured sections of walls, floors, or roofs that are transported to construction sites for assembly. These panels are typically constructed from materials such as wood, steel, or concrete. They are available in a variety of shapes, including sandwich panels, structural insulated panels (SIPs), and curtain wall panels. The prefabrication of these components enables a more efficient and streamlined construction process, thereby reducing on-site labor, waste, and construction time. The Prefabrication Market is experiencing substantial development because of the growing popularity of prefabricated panels. Considering the construction industry's current challenges, including labor shortages, increasing costs, and the demand for sustainable building practices, prefabricated panels provide a viable solution. Their utilization decreases the necessity for skilled personnel on-site, minimizes material waste because of controlled manufacturing environments, and expedites project timelines. Furthermore, prefabricated panels contribute to sustainability by integrating energy-efficient materials and designs, which is consistent with the worldwide initiative to promote more environmentally friendly construction methods. Therefore, the demand for prefabricated panels has been increasing, which has contributed to the overall expansion of the prefabrication market. The increasing significance of prefabricated panels in contemporary construction is being reflected in the emergence of numerous trends. The integration of sophisticated manufacturing technologies, such as automation and robotics, into panel production is a notable trend. These technologies further reduce production costs and lead times by improving precision and efficiency. An additional trend is the growing trend of customizing prefabricated panels to satisfy specific design and performance specifications. This encompasses the creation of more fire-resistant panels that have superior thermal insulation, and superior acoustic properties in order to meet the diverse requirements of industrial, commercial, and residential structures
Global Prefabrication Material Insights
By Material, the market is segmented into Concrete, Steel, Wood, Plastic, and Others. In the Prefabrication Market, concrete is a material that is highly regarded for its versatility, durability, and strength. Prefabricated concrete is the process of producing concrete components, including slabs, beams, and panels, in a controlled factory environment prior to their transportation to construction sites for assembly. This approach is a fundamental component of the expanding prefabrication industry, as it substantially decreases construction time, labor expenses, and material waste.
In numerous keyways, the prefabrication market is being positively impacted by the utilization of prefabricated concrete. Initially, the material's inherent characteristics, including its high compressive strength and fire resistance, render it an optimal choice for the construction of durable and resilient structures. The global demand for cost-effective, rapid construction solutions has increased as urbanization continues to accelerate. Prefabricated concrete effectively satisfies these requirements. Furthermore, prefabricated concrete is frequently manufactured with minimal waste, which is consistent with the increasing emphasis on sustainability in the construction sector. The material's allure is further enhanced by its capacity to recycle and reuse concrete components, which is contributing to market growth as environmental regulations become more stringent. Additionally, the adaptability of concrete enables the creation of a wide range of design options, including intricate architectural forms and basic structures. This adaptability allows architects and engineers to design buildings that are both aesthetically attractive and innovative, thereby increasing the popularity of prefabricated concrete in infrastructure, residential, and commercial projects. Consequently, the prefabrication market has experienced consistent growth, notably in regions such as North America and the Asia-Pacific, where construction activities are on the rise
Global Prefabrication Construction Type Insights
By Construction Type, the market is segmented into Panelized Construction, Modular Construction, Pre-engineered Buildings, Other Construction Type. Modular construction is a critical expression in the Prefabrication Market, as it signifies a substantial change in the design, production, and assembly of buildings. This construction technique entails the production of individual modules or sections of a building in a factory environment, which are subsequently transported to the construction site and assembled into a complete structure. These modules are constructed in accordance with conventional construction methods and are suitable for residential, commercial, and industrial structures. Modular construction significantly contributes to the expansion of the prefabrication market by providing a distinctive combination of sustainability, efficiency, and adaptability.
The modular construction technique is primarily responsible for the expansion of the market by significantly reducing construction time and costs. The production of modules in a controlled factory environment enables the concurrent completion of various stages of construction, including framing, electrical work, and piping, as opposed to the sequential completion of these stages in traditional on-site construction. This overlap has the potential to shorten project timelines by as much as 50%, enabling the completion of buildings in weeks rather than months. Additionally, the construction of these modules indoors reduces weather-related delays, thereby improving the predictability and efficacy of project management. In sectors where rapid development is essential, such as healthcare facilities, educational institutions, and affordable housing initiatives, this time-saving feature is particularly appealing.
The prefabrication market is also significantly influenced by modular construction's cost-effectiveness. The controlled environment of a factory enables more effective resource management, improved overall quality control, and reduced material waste. Furthermore, economies of scale can be realized by concurrently producing numerous modules for a variety of initiatives, thereby reducing per-unit costs. This cost-effectiveness is particularly appealing to investors and developers, particularly in regions with a scarcity of specialized labor or high labor costs. The future of the prefabrication market is being influenced by the trends surrounding modular construction. The increasing emphasis on sustainability is one of the most notable trends. Modular construction is inherently more sustainable than traditional construction methods because of its efficient utilization of energy and materials. The precision of factory production minimizes waste, and any surplus materials can frequently be recycled for future use. In addition, the modular design facilitates the integration of energy-efficient systems, including advanced insulation, energy-efficient windows, and green roofing, thereby reducing operational energy consumption. This trend is consistent with the global demand for sustainable construction solutions and the broader movement toward green building practices
Figure 1: Prefabrication Market, by Construction Type, 2023 & 2032 (USD Million)
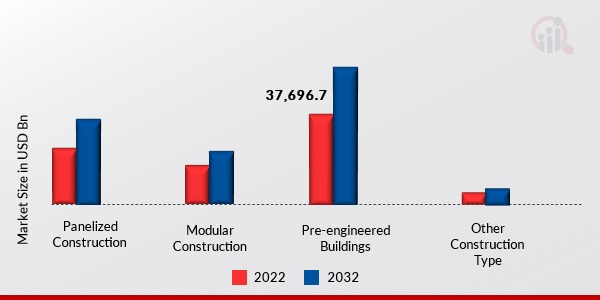
Global Prefabrication Form Insights
By Prefabrication Form, market is segmented into Full and Partial. Partial prefabrication is a construction method that involves the production of specific components or sections of a building in a controlled environment off-site and their subsequent transportation to the construction site for assembly within the context of the Prefabrication Market. Partially prefabricating involves the production of specific elements, such as walls, floors, staircases, or façade panels, off-site, in contrast to complete prefabrication, which involves the creation of entire structures or large modules off-site. These prefabricated components are subsequently incorporated into conventional on-site construction methods. Numerous factors have contributed to the development of the Prefabrication Market, including partial prefabrication. Initially, it provides a compromise between the adaptability of on-site construction and the efficiency of off-site manufacturing. In markets where local regulations, site-specific challenges, or design complexity may render complete modular construction impractical, this equilibrium is particularly appealing. Without fully committing to a modular approach, developers can still accomplish significant time and cost savings, reduce material waste, and improve the quality of construction by prefabricating only certain components.
Global Prefabrication Application Insights
By Application, the market is segmented into Residential and Non-Residential. The utilization of prefabricated construction methods in the construction of residential structures, including residences and apartments, is referred to as "residential" in the Prefabrication Market. Prefabrication is the process of assembling a variety of building components in a controlled environment off-site and subsequently transporting and installing them at the construction site. The numerous benefits of this method, such as reduced construction time, cost savings, enhanced quality control, and environmental benefits, have led to its increasing adoption in residential construction.
The Prefabrication Market has experienced substantial development as a result of the widespread implementation of prefabrication in the residential sector. There is an urgent requirement for construction methods that are scalable, cost-effective, and efficient, particularly in swiftly growing economies, as urbanization accelerates and housing demand increases. Prefabrication addresses these requirements by providing construction timelines that are shorter than those of conventional on-site methods. In regions that are experiencing housing shortages, the capacity to promptly deliver substantial quantities of residential units is crucial.
Furthermore, prefabrication is particularly advantageous in markets where skilled labor is either scarce or costly, as it reduces labor costs. The quality and durability of residential buildings are also improved by the precision of factory-produced components, which reduces maintenance costs and extends the tenure of structures. Additionally, prefabrication is inherently more sustainable due to its ability to integrate energy-efficient materials and designs and its reduced waste generation, which is consistent with the increasing global emphasis on green construction practices.
Global Prefabrication Regional Insights
The report on the Prefabrication Market has been segmented based on region as North America, Europe, Asia-Pacific, Middle East & Africa, and South America. The prefabrication market in North America is undergoing substantial development, which is being fueled by a combination of technological advancements, labor shortages, and the growing demand for sustainable construction practices. The construction industry in the United States and Canada is progressively transitioning to modular and prefabricated building solutions. These solutions provide improved quality control, reduced waste, and faster project timelines. This change is especially apparent in urban areas, where the high demand for residential and commercial spaces necessitates the implementation of more efficient and expedited construction methods.
The ongoing labor scarcity in the construction industry is one of the primary factors driving the prefabrication market in North America. Skilled labor is becoming scarcer, resulting in increased labor costs and project delays. The use of prefabrication facilitates the completion of a greater amount of construction work in controlled factory environments, thereby reducing the necessity for on-site labor and allowing for the automation of tasks. This mitigates these issues. This method not only expedites construction but also reduces the likelihood of delays caused by inclement weather, which is prevalent in numerous regions of North America.
The prefabrication market in the region is also experiencing significant development as a result of technological advancements. The precise planning and execution of prefabricated components are facilitated by the integration of Building Information Modeling (BIM) and advanced manufacturing techniques. This precision results in improved construction quality and minimizes material waste, which is consistent with the increasing emphasis on sustainability in the construction sector. Furthermore, the implementation of green building certifications, including LEED (Leadership in Energy and Environmental Design), is motivating developers to investigate prefabrication as a method of enhancing energy efficiency and minimizing the environmental impact of their projects.
Figure 2: Prefabrication Market, by region, 2023 & 2032 (USD Million)
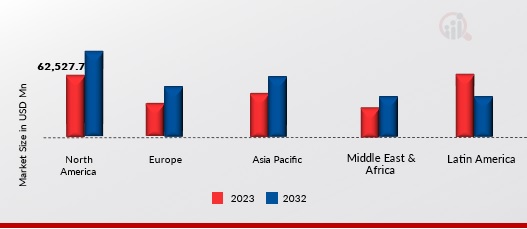
The Nano metrology market in Europe is expected to be one of the leading markets, Nano meteorology in recent years has faced explosive growth in different types of applications. The research and development and number of applications in Nano Metrology keep on growing in the coming years. With the versatility of application, Prefabrication is being used efficiently. The Service National Standards of the FPS Economy plays an essential role in the growth, through specific projects assigned to Prefabrication as well as through on-going research into the best possible efficiency of physical measurements. In impact, on a nonmetric scale, the accuracy of temperature measurements or measurements of electricity or pressure determines the accuracy of the dimensional measurements themselves. The demand for Prefabrication will be on a boom and heading towards the maturity stage where the market will be established. Germany, France, and the United Kingdom are the major markets for Prefabrication in Europe. The growth in these countries is driven by the presence of many leading nanotechnology research institutions and companies. Europe is a significant market for Prefabrication, driven by investments in nanotechnology research and development.
Global Prefabrication Key Market Players & Competitive Insight
The Prefabrication Market is distinguished by its competitive and dynamic landscape, which is driven by the innovation and growth of several key actors across various segments. Prefabrication, or off-site construction, is the process of assembling building components in a manufacturing environment prior to their transportation and installation at the construction site. This method provides a variety of advantages, such as enhanced quality control, cost efficacy, and reduced construction time.
Lendlease Group, Skanska AB, Modular Building Systems Inc., Katerra Inc., and Red Sea Housing Services Company are major players in the prefabrication market. These organizations are the most successful because of their extensive experience, technological advancements, and large-scale initiatives. Lendlease and Skanska are renowned for their high-profile, large-scale projects, which frequently emphasize the integration of sustainable construction practices with prefabrication. Katerra and Modular Building Systems are experts in the development of innovative modular designs that are designed to optimize efficiency and shorten construction timelines. Red Sea Housing Services offers prefabricated solutions that are specifically designed to withstand the harshest environmental conditions, with a focus on adaptability and durability. The market is divided into three categories: product category, material, and application. The primary product categories are modules, frames, and panels. Modules and frames are widely used in a variety of building types, including residential and commercial, due to their efficiency and adaptability. Panels, particularly those constructed from steel and concrete, are preferred due to their durability and strength. The selection of material—whether it be wood, steel, or concrete—influences the cost, environmental impact, and construction pace, fueling competition among manufacturers.
Key Companies in the Prefabrication Market include.
- Riko Hiše d.o.o.
- RED SEA INTERNATIONAL
- Lendlease Corporation
- LARSEN & TOUBRO LIMITED
- Guerdon, LLC
- Barratt Developments PLC
- Skanska
- Clayton
- Daiwa House
- Morton Buildings, Inc.
Global Prefabrication Industry Developments
- In November 2023, Red Sea International signs a $16mln prefabricated building contract for Aramco’s Jafoura project.
- In November 2023, Red Sea International inks SAR 43.9 mn contract for prefabricated buildings in Jubail.
- In March 2024, Colorado Welcomes Guerdon’s Expansion to Meet Surging Demand for Modular Housing.
Prefabrication Market Segmentation
Prefabrication Market by Product Type Outlook (USD Million, 2019-2032)
- Panels
- Modules
- Frames
- Girders
- Others
Prefabrication Market by Material Outlook (USD Million, 2019-2032)
- Concrete
- Steel
- Wood
- Plastic
- Others
Prefabrication Market by Construction Type Outlook (USD Million, 2019-2032)
- Panelized Construction
- Modular Construction
- Pre-engineered Buildings
- Other Construction Type
Prefabrication Market by Prefabrication Form Outlook (USD Million, 2019-2032)
Prefabrication Market by Application Outlook (USD Million, 2019-2032)
- Residential
- Non-residential
Global Prefabrication Regional Outlook
- North America
- US
- Canada
- Mexico
- Europe
- Germany
- France
- UK
- Spain
- Italy
- Switzerland
- Netherlands
- Russia
- Rest of Europe
- Asia-Pacific
- China
- Japan
- India
- South Korea
- Rest of Asia-Pacific
- Middle East and Africa
- Saudi Arabia
- UAE
- South Africa
- Rest of MEA
- Latin America
- Argentina
- Brazil
- Peru
- Rest of South America
Report Attribute/Metric |
Details |
Market Size 2023 |
USD 2,11,400.0 Million |
Market Size 2024 |
USD 2,24,612.5 Million |
Market Size 2032 |
USD 3,47,846.2 Million |
Compound Annual Growth Rate (CAGR) |
5.62% (2024-2032) |
Base Year |
2023 |
Market Forecast Period |
2024-2032 |
Historical Data |
2019- 2022 |
Market Forecast Units |
Value (USD Million) |
Report Coverage |
Revenue Forecast, Market Competitive Landscape, Growth Factors, and Trends |
Segments Covered |
by Product Type, by Material, by Construction Type, By Prefabrication Form, by Application |
Geographies Covered |
North America, Europe, Asia-Pacific, Middle East & Africa, and South America. |
Countries Covered |
The U.S., Canada, Mexico, Germany, France, Italy, Spain, UK, Switzerland, Netherlands, Russia, Rest of Europe, China, India, Japan, South Korea, Rest of Asia Pacific, Saudi Arabia, UAE, South Africa, Rest of MEA, Argentina, Brazil, Peru, Rest of South America |
Key Companies Profiled |
Riko Hiลกe d.o.o., RED SEA INTERNATIONAL, Lendlease Corporation, LARSEN & TOUBRO LIMITED, Guerdon, LLC, Barratt Developments PLC, Skanska, Clayton, Daiwa House, Morton Buildings, Inc. |
Key Market Opportunities |
ยทย ย ย ย ย ย The construction of educational facilities is another promising opportunity for the Prefabrication Market |
Key Market Dynamics |
ยทย ย ย ย ย ย The increased demand for sustainable and energy-efficient building solutions is a significant driver of the Prefabrication Market |
Frequently Asked Questions (FAQ) :
The Prefabrication Market size is expected to be valued at USD 3,47,846.2 Million in 2032.
The global market is projected to grow at a CAGR of 5.62% during the forecast period, 2024-2032.
Asia Pacific had the largest share of the global market.
The key players in the market are Riko Hiše d.o.o., RED SEA INTERNATIONAL, Lendlease Corporation, LARSEN & TOUBRO LIMITED, Guerdon, LLC, Barratt Developments PLC, Skanska, Clayton, Daiwa House, Morton Buildings, Inc.