Top Industry Leaders in the Injection Molding Machinery Market
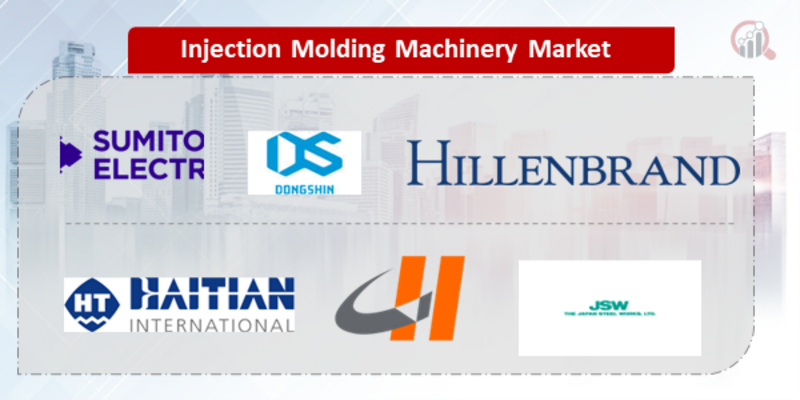
*Disclaimer: List of key companies in no particular order
Top listed global companies in the industry are:
- HAITIAN International (China)
- SUMITOMO Heavy Industries (Japan)
- JAPAN Steel Works (Japan)
- Chen Hsong Holdings (Hong Kong)
- Hillenbrand Inc.(US)
- Dongshin Hydraulic (South Korea), and others.
Shaping Plastic: The Competitive Landscape of the Injection Molding Machinery Market
The injection molding machinery market, responsible for shaping the plastic landscape of countless products, hums with fierce competition. Understanding the strategies, trends, and factors influencing this dynamic market is crucial for manufacturers navigating towards success.
Key Players and their Strategies:
- Global Giants: Industry titans like Engel, Milacron, and Sumitomo Demag leverage their extensive global reach, diverse product portfolios, and technological prowess to maintain market leadership. Engel, for instance, focuses on high-performance electric machines and advanced automation solutions.
- Regional Powerhouses: Regional players like Chen Hsong (Taiwan), Haitian International (China), and Arburg (Germany) cater to specific regional needs and price sensitivities with efficient and cost-effective machines. Haitian International's rapid production and competitive pricing exemplifies this strategy.
- Specialization Champions: Companies like Netstal (Switzerland) and Toshiba Machine (Japan) carve niches by specializing in high-precision or high-performance machines for demanding applications like medical or optical products. Netstal's expertise in micro molding for medical devices showcases this specialization.
Factors for Market Share Analysis:
- Machine Technology: Innovation in clamping force, injection unit precision, and energy efficiency directly impacts production output, product quality, and operating costs. Milacron's focus on hydraulic servo technology and Sumitomo Demag's emphasis on all-electric machines demonstrate this emphasis.
- Material Handling and Automation: Integrated automation systems for material handling, mold changing, and robot integration optimize production times and minimize labor costs. Arburg's robotic systems and Engel's automated mold changing solutions highlight this trend.
- Software and Connectivity: Advanced software for process control, data analysis, and predictive maintenance enables real-time optimization, improves machine uptime, and reduces scrap rates. Chen Hsong's focus on smart manufacturing platforms and Toshiba Machine's integration of AI-powered process control are prime examples.
- Sustainability Focus: The demand for eco-friendly solutions drives development of energy-efficient machines, use of recycled materials, and reduced waste generation. Engel's Ecodrive energy recovery system and Haitian International's focus on energy-efficient hydraulics exemplify this commitment.
Emerging Trends and Company Strategies:
- Additive Manufacturing Integration: Combining injection molding with 3D printing opens up new design possibilities and enables hybrid manufacturing for complex parts. Netstal's integration of 3D printing technology showcases this trend.
- Digital Twins and Virtual Molding: Creating digital simulations of molding processes and machines allows for virtual optimization, reducing development time and improving product quality. Toshiba Machine's focus on digital twin technology exemplifies this.
- Subscription and Service Models: Shifting from traditional sales models to subscription-based services and comprehensive maintenance packages is gaining traction, providing predictable costs and ensuring optimal machine performance. Milacron's "Molding as a Service" offering is a prime example.
- Partnerships and Collaborations: Partnerships between machinery manufacturers, material suppliers, and software providers are fostering innovation and accelerating market penetration. Sumitomo Demag's collaboration with BASF on materials for lightweighting applications demonstrates this approach.
Overall Competitive Scenario:
The injection molding machinery market is a dynamic and complex landscape, fueled by technological advancements, cost pressures, and sustainability concerns. Success hinges on continuously refining key strategies like technological leadership, cost-effectiveness, service excellence, and adaptability. Building collaborative ecosystems, embracing disruptive technologies like digital twins and additive manufacturing, and prioritizing sustainability are essential for navigating the competition and shaping the future of plastic production.
Latest Company Updates:
July 2023
Haitian International has set up a formal ceremony to inaugurate its state-of-the-art manufacturing facility for injection molding machines in Mexico.
The new site, which represents an investment of approximately $50 million, includes 92,000 m2 (990,000 ft2) of space for manufacturing, sales, and administration. About 27,000 m2 (290,000 ft2) of that is used for production, including tasks like metalworking, assembly, and customer service. More than 100 machines have been made and supplied to local clients. The recently constructed structure is located in Centro Logistico Jalisco, a business park in the municipality of Acatlan de Juarez, Guadalajara, Mexico.
April 2023
A 20-ton iM18E compact hybrid injection moulding machine with a minuscule 88 by 30 inch footprint, has been released by the Japanese firm Sumitomo Heavy Industries Ltd. (SHI). For molding connections, precision gears, and other electronic parts, the iM18E was designed with a maximum injection speed of 600 mm/sec. Only Japan and other Asian regions would currently be able to purchase the technology, a company representative said.
The SE18DUZ, a variant identical to the iM18E offered by SHI, reportedly occupies 21% less space. The iM18E requires considerably less floor space because of an updated injection unit and a machine frame that allows supplementary equipment to be placed underneath the machine.
The iM18E has an electronic plasticizing unit with a hydraulic direct-pressure clamp and a low-inertia servomotor. When powered by the ISCII direct-drive system, SHI asserts that the shot-to-shot weight variance of the iM18E is reduced to roughly one-third of that of an equivalent hydraulic machine. The hybrid design reportedly consumes 50% less energy than equivalent hydraulic machinery.