Top Industry Leaders in the CNC Controller Market
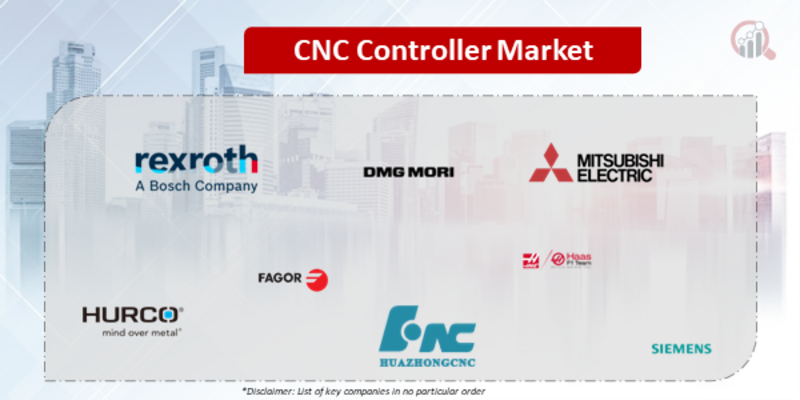
The Competitive Landscape of the CNC Controller Market
The CNC controller market stands as the brains behind the brawn of modern manufacturing. These sophisticated systems orchestrate the intricate movements of computerized numerical control (CNC) machines, shaping raw materials into precise components with unwavering accuracy. Understanding the competitive landscape in this dynamic market is crucial for players seeking to guide the future of precision engineering.
Some of the CNC Controller companies listed below:
- Siemens AG
- Mitsubishi Electric Corporation
- Bosch Rexroth AG
- DMG Mori Co Ltd
- Hurco Companies Inc
- Fagor Automation Corporation
- Haas Automation, Inc.
- Wuhan Huazhong Numerical Control Co., Ltd.
- Yamazaki Mazak Corporation
- FANUC Corporation
- Okuma Corporation
Strategies Adopted by Leaders
- Technological Prowess: Leading players like FANUC, Siemens, and Mitsubishi Electric invest heavily in R&D, pushing boundaries in processing power, advanced motion control algorithms, and open-source platforms. They pioneer technologies like multi-axis machining capabilities, real-time collision avoidance, and cloud-based connectivity, offering enhanced performance, flexibility, and remote monitoring.
- Application Focus: Players cater to specific industry segments. Haas Automation excels in affordable CNC machines for small and medium-sized businesses, while DMG MORI focuses on high-performance solutions for aerospace and automotive applications. This specialization allows for tailored features and deeper understanding of each sector's unique needs.
- Ease of Use and Programming: User-friendly interfaces and intuitive programming languages are critical for attracting new users and simplifying production processes. Companies like Fagor Automation and Okuma concentrate on offering user-friendly interfaces and powerful yet easily programmable control systems.
- Global Footprint: Establishing geographically diverse sales and service networks is crucial for catering to the global nature of manufacturing. Heidenhain and Bosch Rexroth maintain strong regional presence across continents, ensuring customer proximity and efficient support.
- Strategic Partnerships: Collaborations with machine tool manufacturers, software developers, and automation specialists accelerate innovation and broaden market reach. For instance, partnerships between controller providers and cutting-tool companies enable seamless integration of tool libraries and optimized machining parameters.
Factors for Market Share Analysis:
- Controller Features: Analyzing market share by controller features (number of axes, processing power, connectivity options) reveals dominant players in each segment and future growth potential. Advanced controllers with multi-axis machining capabilities and cloud connectivity are gaining traction, catering to complex machining demands and Industry 4.0 integration.
- End-User Industry: Understanding the needs of different end-user segments (aerospace, automotive, medical) is key. Aerospace applications prioritize high precision and reliability, while medical device manufacturing demands stringent hygiene and safety regulations. Players cater their features and capabilities to meet these diverse requirements.
- Price Point: Price remains a crucial factor, particularly for smaller businesses. Companies like Mazak and Hurco offer affordable CNC machines and controllers, catering to the budget-conscious segment of the market.
New and Emerging Companies:
- Open CNC: This open-source hardware and software platform aims to democratize CNC technology by providing affordable and customizable controller solutions, catering to the growing maker community and educational institutions.
- EtherCAT: This industrial communication protocol is gaining traction in CNC controllers due to its high speed, real-time capabilities, and flexibility. Companies like Beckhoff Automation are integrating EtherCAT technology into their controllers, offering enhanced performance and interoperability.
- Cloud-Based CNC Platforms: The rise of cloud-based platforms for CNC data management and remote monitoring is creating new opportunities for players like Sinumerik Integrate by Siemens, offering enhanced production visibility and remote support capabilities.
Industry Developments:
Sept. 07, 2023- Okuma America Corporation launched its next-generation CNC machine control, OSP-P500, for its expansive line of CNC machine tools. The new control, Okuma OSP-P500, is the company's latest innovation within its OSP control line. Leveraging the OSP line's expertise and the latest digital transformation technologies, the OSP-P500 can enhance user experiences and fully optimize modern manufacturing operations.
Jul. 14, 2023- E-CAT CNC launched a revolutionary CNC-enabled fiber laser machining controller that can set a new standard for precision, versatility, and affordability. LaserCAT is based on Newfangled's MACH4 CNC controller, allowing it to embrace EtherCAT by utilizing IntervalZero's KINGSTAR fieldbus powered by EtherCAT. Laser CAT is the ultimate solution for CNC machines to help builders embrace EtherCAT and meet the evolving demands of the thermal cutting industry.
May 16, 2023- Heidenhain showcased its new CNC control system, the TNC7, at Eastec 2023. The TNC7 provides a customizable user experience by offering intuitive operation and a virtual simulation of the machined part and work envelope. The new TNC7 CNC control will be the basis of future control generations from Heidenhain. In addition to a new look and feel, this control features upgraded hardware components, including a 24" HD touchscreen monitor and an advanced, adaptable user interface.
May 16, 2023- Siemens Industry Inc. showcased its expanded Sinumerik One digital-native CNC at Eastec 2023. Sinumerik One is designed to simplify operation, reduce machine wear and increase productivity. This new control generation uses upgraded software and hardware to enable machine builders and end-users to gain a full digital twin of the machine tool and machining sequences. According to Siemens, its Sinumerik One machine tool control system can be used for digital transformation to boost productivity and flexibility in a modular way.