Top Industry Leaders in the Plastic Processing Machinery Market
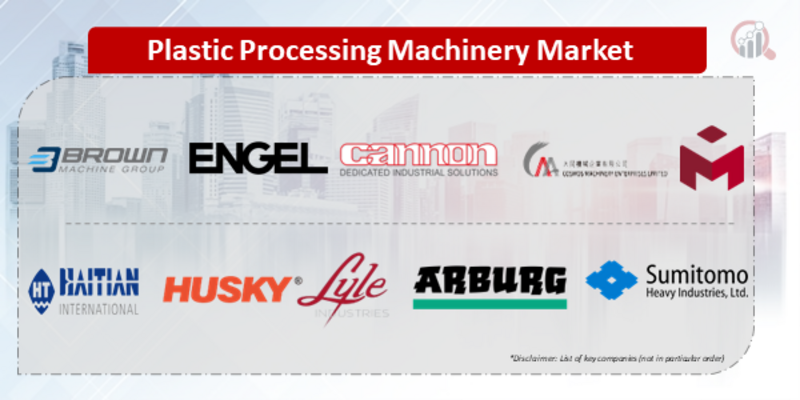
*Disclaimer: List of key companies in no particular order
Top listed global companies in the industry are:
- Brown Machine Group (US)
- Haitian International Holdings Limited (China)
- Milacron (US)
- ENGEL AUSTRIA GmbH (Austria)
- Husky Injection Molding Systems Ltd (Canada)
- Lyle Industries (US)
- ARBURG GmbH (Germany)
- Cannon S.P.A. (Italy)
- Cosmos Machinery Enterprises Limited (Hong Kong)
- Sumitomo Heavy Industries (Japan), and others.
Shaping the Polymer Landscape: A Deep Dive into the Plastic Processing Machinery Market
The plastic processing machinery market is a fiercely competitive arena where established giants clash with agile innovators. Understanding the strategies shaping this dynamic landscape, the factors governing market share, and emerging trends is crucial for navigating this ever-evolving marketplace.
Key Players and their Strategies:
- Global Titans: Industry titans like Engel, Arburg, and KraussMaffei leverage their extensive product portfolios, technological prowess, and established global networks to cater to diverse applications. Engel excels in injection molding machines, Arburg focuses on complex applications with its ALLROUNDER machines, and KraussMaffei dominates blow molding solutions. Their strategy rests on continuous innovation, offering a comprehensive range of machinery, and providing strong after-sales support.
- Regional Dominators: Companies like Chen De Plastics Machinery and Yizumi Heavy Machinery Co. hold sway in specific geographies by tailoring solutions to regional regulations and cost sensitivity. Chen De caters to China's high-demand market with cost-effective options, while Yizumi focuses on energy-efficient solutions for Southeast Asia. Their success hinges on understanding regional needs and offering cost-competitive solutions.
- Niche Disruptors: Startups like NextGen Machinery and AMK Automation disrupt the market with cutting-edge solutions. NextGen focuses on advanced additive manufacturing machines for plastics, while AMK provides automation solutions for optimized production lines. Their strategy revolves around offering specialized solutions, often leveraging digitalization and automation, to address emerging needs.
Factors for Market Share Analysis:
- Technological Leadership: Offering advanced processing technologies like multi-component injection molding, closed-loop control systems, and Industry 4.0 integration empowers players to address demanding applications and attract tech-savvy customers.
- Industry Expertise: Deep understanding of specific end-uses, such as packaging, automotive, or medical devices, enables tailoring solutions for optimal performance and regulatory compliance. Arburg's specialized medical applications machines exemplify this expertise.
- Cost-Effectiveness and ROI: Maintaining a balance between advanced features and affordability is crucial, especially in price-sensitive segments. Regional specialists like Chen De often win through cost-competitiveness.
- Global Presence and Service Network: Establishing a strong global footprint with readily available parts and after-sales support fosters customer trust and facilitates rapid deployment. KraussMaffei's extensive service network is a key advantage.
Emerging Trends and Company Strategies:
- Sustainability Focus: Eco-friendly solutions with reduced energy consumption, bio-based materials compatibility, and circular economy principles are gaining traction. Engel's eco-friendly machines address this growing demand.
- Digitalization and Connectivity: Integrating sensors, data analytics, and cloud platforms into machinery enables real-time process monitoring, predictive maintenance, and remote diagnostics. NextGen's connected machinery exemplifies this trend.
- Modular and Scalable Systems: Offering modular machine designs and flexible control systems allows for adaptation to varied production needs and future growth. AMK's automation solutions cater to this growing need for agility.
- Focus on Additive Manufacturing: The integration of additive manufacturing technologies like 3D printing into plastic processing opens new possibilities for complex shapes and customization. NextGen's focus on this area positions them strategically.
Overall Competitive Scenario:
The plastic processing machinery market is a dynamic landscape where established players compete with regional specialists and technology-driven startups. Success hinges on continuous innovation, industry expertise, a global reach, and adapting to emerging trends. Companies embracing sustainability, digitalization, modularity, and additive manufacturing hold a strong hand in shaping the future of this ever-evolving industry. However, navigating this landscape requires careful consideration of regional dynamics, raw material price fluctuations, and the specific needs of target markets.
Latest Company Updates:
October 2023- A group of young Abergavenny students are turning trash into treasured items in a pioneering eco-project launched to get more girls interested in science subjects. The students from King Henry VIII 3-19 School are part of a lunchtime club named The Plastics Lab and are turning bottle tops made from HDPE plastic into jewelry, coasters, key rings, and bookmarks. These are sold at markets and fairs with the hope of making money to invest in more equipment for their department and expand their work. Teacher and project leader Raine Arken said that they want to make their school as eco-friendly as possible. She further added that they noticed there was a lot of plastic being thrown away or littered, so they decided to do something about it and recycle it. The club started in 2022 with just two members as part of a STEM project (Science, Technology, Engineering and Mathematics)
June 2023- Italy-based Bausano & Figli S.p.A. says its Nextmover line of twin-screw extruders is ready for delivery, equipped with a multidrive system, which it says offers maximum efficiency and longevity of mechanical components. Bausano, a designer, and producer of customized extrusion lines for the transformation of plastic materials, says its patented multidrive transmission is the result of years of research and experimentation. The system features four shafts, each governed by a motor. The company says that this composition ensures that the torque stress is distributed over four points in favor of lower stresses on the drive shaft, screws, and gears and higher torque for less power installed on each motor, adding that the resulting benefits include reduced risk of failure, the increased average life of the machine itself and low energy consumption.