Pune, India, March, 2023 /press release/- Market Research Future Published a Cooked Research Report on Global High pressure seals Market Research Report.
High Pressure Seals Market Highlights
The High Pressure Seals market share is likely to attain a global CAGR of 6.82% during the ongoing forecast period of 2022-2030. The global High Pressure Seals market was valued at USD 4.86 billion in 2021 and is projected to reach USD 8.78 billion by the end of 2030.
A mechanical seal is defined as a device which helps to join systems or mechanisms together by preventing leakage, containing pressure, or excluding contamination. High pressure sealing can be defined as sealing which confine fluids at pressures above 5,000 psi. Materials used in high pressure sealing possess properties such as hardness, sufficient tear strength, and modulus to prevent extrusion through the gap.
The major factors driving the global market growth are Robust growth in oil & gas industry and expanding aerospace & defense industry.
Competitive Landscape
Several regional and local vendors are present in the global high-pressure seals market. The regional market is extremely competitive, with all competitors vying for a greater market share. Vendors compete on price, product quality, dependability, and aftermarket services. To survive and flourish in a competitive market climate, suppliers must produce cost-effective and efficient products.
EagleBurgmann, Gallagher Seals, Performance Sealing Inc (PSI), FTL, Trelleborg, James Walker, John Crane, Kalsi Engineering, Inc., Parker Hannifin Corp, Flowserve Corporation, F.lli Paris S.r.l., Bal Seal Engineering are the market's major players, competing in terms of the variety of applications and components, as well as efficiency, reliability, affordability, and advanced technology. The players' key objective is to deliver sophisticated items to aid in growing acceptance, which might help boost a country's growth with advanced products. Although global firms dominate the industry, a few regional and smaller local businesses with a small market share are also active.
The leading companies are projected to grow their presence and solutions in these countries throughout the forecast period through mergers and acquisitions of local and regional players. As a result, suppliers must create new technologies to keep up with developing technological trends that may influence the market competitiveness of their product lines.
Segmentation
By Material
- Elastomers: Various types of elastomers such as polyurethane, Acrylonitrile-Butadiene Rubber, Fluoro Rubber, Ethylene Propylene Diene Rubber (EPDM), and Hydrogenated acrylonitrile butadiene rubber (HNBR), among others are used in the manufacturing of high pressure seals. Right choice of seal material is very critical in sealing systems to operate leak free and to maintain a long service life. Seal design and material performance are the two most key factors in terms of having the best sealing solution. Elastomers are one of the most widely used seal material. They exhibit high resilience, elasticity, and chemical resistance that are suitable for sealing applications. Most elastomeric seals are developed to operate within ambient temperature to about 1,500 psi. At very high pressures, the seal can have adequate strength to resist extrusion into the clearance gap.
- Metals: Metal seals are prominently used in most extreme environments. Resilient metal seals cater the challenges of cryogenics or high temperatures, or corrosive chemicals, hard vacuum, and high levels of radiation performing dependably every year. In high pressure applications, the primary choice is metal seals as they offer good leak tightness and have the capacity to sustain high pressures. Also, they find usage in applications with pressures as high as 6000 bar. They possess higher design flexibility to solve critical issues regarding pressure, temperature, leak rate, fire safety, and process compatibility. With increasing stringent leakage and pollution regulations coupled with the demand for lifetime reliability and higher efficiency, metal seals offer the highest integrity solution.
- PTFE: PTFE high pressure sealing solutions are developed to withstand aggressive environment, high pressures, high temperatures, and dry running which traditional seals made of elastomeric sealing materials cannot withstand. It exhibits excellent chemical resistance, withstands dry running, wide operating temperature range, withstands pressures up to 500 psi, thus making it suitable for demanding applications. It is predominantly used in compressors, oilfield equipment, hydraulic actuators, brake systems, mechanical seals, aircraft engines, food processing equipment, etc. It further provides numerous benefits for fluid power applications when standard elastomer seals cannot offer a sealing solution. The material is impermeable to any form of harm a hydraulic system can face. Contamination, heat, and friction are not a suitable match for a PTFE seal, specifically with the already limited bounds these systems operate in.
- Rubber-Metal Combination: Rubber-bonded to metal to create a composite seal lowers mechanical vibration, reduces assembly costs, makes installation easier, and lowers noise. Rubber-to-metal bonded parts offer a special type of seal. Majority of metals can be used to be bonded to rubber to produce rubber metal bonded parts. However, market players are required to ensure that the right metal is used with right type of rubber for suitable applications. Various types of rubbers which can be commonly bonded to metals are neoprene, natural rubber, silicone, FKM, etc. These seals exhibit high economic and technical efficiency along with high sturdiness of the base component and high resilience. Suitable metal substrates used are brass, stainless steel, aluminum, steel, etc. It offers a long-term and a dependable seal between multiple surfaces.
- Others: The others segment was valued at USD 244.07 million in 2021 and is estimated to grow at a CAGR of 5.06% during the forecast period. The other segment include PEEK, carbon graphite, polyimide, etc.
By Application
- Pumps: Pumps are one of the widely used equipment in petrochemical, oil & gas, chemical, etc. Pumping equipment is extremely diverse, varying in size, type, materials, driver of construction. Whether the refinery is transforming crude into consumer and industrial products, circulating water to generate electricity, transporting gas through miles of pipeline, or cool a heat exchanger, one needs a dependable solution. The reliability of mechanical seals, high pressure pumps, and seal support systems are highly critical to effective and safe operations. The mechanical seal acts as a slider bearing and a check valve. It prevents liquid under pressure from leaking out of the pump, or from drawing air into the pump when under vacuum conditions.
- Valves: Valves direct, regulate, and control the flow of a fluid through numerous passageways from areas of higher pressure to lower pressure. There are various valve configurations that involve both linear and rotary movement. Pressure seal valves are developed for high temperature and high pressure applications such as chemical/industrial processing plants, steam generation stations, and thermal power generating plants across the globe. Piston seals helps in preventing leakage across internal portions of the valve. Rod seals prevents leakage into the environment across the valve shaft. High pressure seals are widely used in check valves, relief valves, ball valves, servo valves, cartridge valves, poppet valves, solenoid valves, and sandwich plate valves, among others.
- Compressors: A compressor is an equipment which increases the pressure of a gas by reducing the volume of the substance. They are widely used in applications which involve increasing the pressure inside a gas storage or a container. They engage in high pressure and demanding environment, thus use high pressure seals. Most commonly applications include cabin pressurization in airplanes, compression of gases in chemical plants & petroleum refineries, filling tires, storage of gas in high pressure cylinders, and air storage for underwater activities. In addition, compressors are predominantly used in gas turbines, refrigeration & air conditioners, pipeline transports of natural gas, rail vehicle operation, and powering pneumatic tools which again operate in a extremely high pressure environment.
- Pipes: Pipeline and pumps are most commonly used products used in the transmission of various types of fluids and gases. Many pipelines are developed to transport gases for fluids over long distance. Furthermore, they also have to deal with issues such as high operating pressures, corrosion, ground shifting, and thermal expansions. All these challenges can cause damage to the pipeline and leakage is highly prevalent. Pipe high pressure seals provide various contact points for added sealing capability. The flexible sealing lip technology enables seals to function during extreme pipe OD to bore misalignment. Pipe seals are available in different materials to cater the temperature and fluid compatibility requirements of the usage. Common application pressures reach up to around 250 psi, but with an integral seal backup ring, they can be for applications with pressures up to 3,000 psi. High pressure seals in pipes are used in a myriad range of industries including agricultural, automotive, and industrial applications such as filter neck seals, coolant lines, fluid transfer, turbo charger pipes, and fill tubes.
- Ducts: Leaky ducts in high pressure applications can reduce cooling and heating system efficiency by as much as 20%. Insulating and sealing ducts lowers your energy bills, improves efficiency, and can pay for itself in energy savings. A duct system which is well-designed and effectively designed can make home and industrial sites more energy efficient, more comfortable, and safer. Sealing and insulating ducts can help with common comfort problems such as room which are too cold in the winter or too hot in the summer.
- Others: The other segment was valued at USD 348.25 million in 2021 and is estimated to register a steady CAGR of 5.58% during the review period. The others segment includes agitators, reactors, heat exchangers, etc.
By End-use Industry
- Oil & Gas: In the oil & gas sector, the equipment used is pushed to greater limits, thus, there is a growing need for more robust, durable, and strong sealing solutions. High-performance seals increasingly gaining popularity in this industry owing to its high strength and high reliability in extreme environments. These seals ensure safety, reliability, and efficient operation of a broad range of onshore and offshore equipment in different conditions- such as various climatic and geographic conditions. In well drilling, completion and production applications, they have to handle system pressures ranging from 5,000 to 30,000 psi, resist aggressive fluid media, salt water and sour gas as well as injection the injection of hot steam. Here, high-temperature seals ensure that the efficiency of drilling operations are not affected. Growing oil & gas exploration activities across the globe coupled with an increasing demand for oil & gas products are likely to boost the segment growth.
- Aerospace and defense: Metal seals are prominently used in aerospace & defense sector, which offer a design option for critical low-duty-cycle, all metal sealing in mission critical applications. Seals in high pressure and high-temperature environment excel under extreme environments such as in engine and moving parts in an aircraft. High pressure seals in aerospace applications are widely used in engine, airframe, avionics, fuel systems, landing gear, flight controls & hydraulics, wheels & brakes, and pneumatic systems. With the present rate of growth of gas turbine engines in the aerospace sector, the development of advanced and efficient sealing technology to cater to the extreme operating conditions of the aero-engines is critical. In addition to designing low-leakage, well-performing, and long-lasting seals, it is vital to maintain them. High pressure seals play a critical role in enhancing engine efficiency at a high performance to cost ratio. Also, increasing air traffic, growing investment in defense to bolster military power, emergence in advanced technologies in aerospace & defense sector, etc. augments the segment growth.
- Power Generation: Power generation industry is emphasizing on improving efficiency and reduce emissions, seals play a key role. Metal seals handle high pressures which optimizes performance and ensures high reliability in this sector, especially used in natural gas power generation. Power generation equipment deploys different types of seals such as grease seals, bearing seals, rotary seals, and oil seals. Spring-energized C-seals, metal E-seals, and lip seals are commonly used to address high pressure in the combustion system where air and fuel are mixed and combusted to create high pressure & temperature gas stream to turn the turbine. Also, V-seals, segmented E-seals, and turbo seals are used to seal the shroud section of the turbines where high pressure gas stream from the combustion system to drive the turbine blades. Increasing demand for power from varied verticals is likely to boost the segment growth.
- Chemical: No industrial production plant can be operated without seals. Chemical plants are required to seal chemical equipment. The number of sealing spots and media to be controlled is large. So, there are significantly large number of plant components which needs to be sealed, including agitators, pumps, compressors, pipes, and ducts carrying liquids and gases. These seals can be widely used in manufacturing and processing, during the handling of inorganic basic chemicals and aggressive chemicals. Moreover, in offering the critical links between pumps and processing equipment in various types of chemical plants, piping arrays should transport high pressure, abrasive high temperature, and otherwise hazardous materials. The flange sealing solutions play a key role in ensuring high safety and reducing downtime.
- Automotive: Seals are critical for automotive sector. They enable a vehicle and its engine to function smoothly. These components are widely used in trucks, motorcycles, passenger vehicles, etc. They help in enclosing gases and liquids in a chamber. Also, they provide protection to bearings, keeps away dust, different gases, liquids, and other contaminants from the integral parts of the component. Automotive industry primarily uses two types of seals, namely O-ring seals and injection molded & lathe-cut seals. O-rings are made of elastomeric materials. They are mainly used to seal two surfaces and can function efficiently in extreme pressures and temperatures, in the presence of gases and liquids. The latter type is superior than the traditionally available seals. Rubber seals offer cushioning and prevents gases and liquids from leaking.
- Pharmaceutical: Hygiene and cleanliness are the most key factors in the pharmaceutical industry. Sealing solutions in this sector are required to prevent contamination, thus ensuring the safety of the medicine. Proper sealing of joints is highly critical to reduce contamination. They are used in reactor vessels, autoclave, pipe joints, driers, and evaporators. Seals are engineered to cater the demanding pressure, temperature, and chemical requirements of specialized and challenging applications, such as centrifuges, bioreactors, etc. Pressure in various pharmaceutical sealing applications is not critical for the material selection but is vital for understanding the duty cycle as many applications switch between vacuum and pressure, which, in turn impacts the dynamic forces on the seals.
- Others: The others segment was valued at USD 118.11 million in 2021 and is estimated to register a steady CAGR of 4.80% during the forecast timeline. The others segment includes water treatment, mining, pulp & paper, etc.
By Region
- North America: The North American market was valued at USD 1,756.90 million in 2021 and is estimated to register a healthy CAGR during the assessment period. This is mainly attributed to presence of well-established end-use industries such as aerospace & defense, oil & gas, automotive, chemical, and pharmaceutical. The US is the key oil & gas producing country in the region and has a robust demand for high pressure sealing solutions in extreme oil drilling activities. Growing demand for oil production from different verticals is expected to bolster the regional market growth. Moreover, strong presence of aerospace companies such as Boeing, Lockheed Martin, and Northrop Grumman, etc. coupled with increasing air traffic are expected to further boost the regional demand for high pressure seals. Furthermore, supportive government policies for increasing efficiency in power generation propels the product demand in the coming years.
- Europe: The European market held a substantial share of 28.37% in 2021 and is projected to reach USD 2,571.19 million by the end of 2030. France, Germany, and the UK are the key contributors in the region. The regional growth is mainly attributed to robust automotive and aerospace & defense industry. Europe is an automotive hub and is known for its popular brands such as Audi, Daimler, Mercedes, etc. Strong automobile production coupled with growing need for efficiency in automobile are expected to bolster the regional market growth. Also, Airbus, a major aircraft manufacturer in the region is increasingly adopting high pressure sealing solutions in aircrafts and military vehicles. Moreover, strong military spending in manufacturing military vehicles along with expanding chemical processing sector in France, Germany, and the UK boosts the usage of high pressure seals. In addition, the oil & gas industry in the region is witnessing a robust growth rate, mainly in Russia, which further uses sealing solutions in oil drilling activities.
- Asia Pacific: The Asia-Pacific market garnered a significant share of 22.63% in 2021 and is estimated to grow at a robust CAGR of 7.85% during the forecast timeline. China is the dominating country market in the region. Strong presence of end-use industries such as chemical, automotive, pharmaceutical, and oil & gas in China, India, and Japan is a key factor augmenting the demand for high pressure seals. Rapid urbanization and expanding industrialization have driven the need for better mobility, chemical products, medicines, and fossil fuels, which further boosts the regional market growth. Also, growing investment in oil & gas exploration activities in emerging countries of India and Indonesia, offers significant opportunities to the oil & gas companies. Moreover, rising automobile production as well as increasing electric vehicle adoption rate bolsters the product demand.
- Latin America: The Latin America market was valued at USD 206.61 million in 2021 and is likely to reach USD 301.15 million during the assessment period. Brazil and Mexico are the key contributing countries in the region. Rising industrialization, growing oil demand, increasing purchasing power, etc. bolsters the sales of automobiles. Seals play a key role in preventing leakage in auto parts, thus witnesses strong demand in passenger vehicles and commercial vehicles. In addition, supportive government policies in improving oil exploration activities further bolsters the regional market growth.
- Middle East & Africa: The Middle East & Africa segment held a substantial share of 8.61% in 2021 and is projected to reach USD 676.66 million during the forecast timeline. Oil & gas is one of the key major industries in the region where Saudi Arabia, Qatar, Kuwait, etc. play a major role in oil drilling operation, thus witness a growing need for high pressure seals. Also, increasing investments in oil & gas drilling and exploration activities further boosts the regional market growth. In addition to this, expanding automobile and power generation sector in the region coupled with supportive government incentives bolster the usage of high pressure sealing solutions.
Read More This Report: High Pressure Seals market share
Leading companies partner with us for data-driven Insights
Kindly complete the form below to receive a free sample of this Report
Base Year | 2023 |
Companies Covered | 15 |
Pages | 140 |
Certified Global Research Member
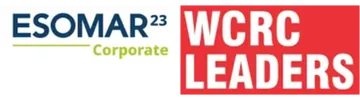
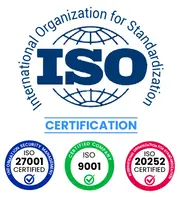
Why Choose Market Research Future?
- Vigorous research methodologies for specific market.
- Knowledge partners across the globe
- Large network of partner consultants.
- Ever-increasing/ Escalating data base with quarterly monitoring of various markets
- Trusted by fortune 500 companies/startups/ universities/organizations
- Large database of 5000+ markets reports.
- Effective and prompt pre- and post-sales support.
Tailored for You
- Dedicated Research on any specifics segment or region.
- Focused Research on specific players in the market.
- Custom Report based only on your requirements.
- Flexibility to add or subtract any chapter in the study.
- Historic data from 2014 and forecasts outlook till 2040.
- Flexibility of providing data/insights in formats (PDF, PPT, Excel).
- Provide cross segmentation in applicable scenario/markets.