Market Research Future (MRFR) has published a cooked research report on the “global aerospace aluminium market” that contains the information from 2018 to 2032.
The Aerospace Aluminium market is estimated to register a CAGR of 7.2% during the forecast period of 2024 to 2032.
MRFR recognizes the following companies as the key players in the global Aerospace Aluminium market— Alcoa Corporation, Constellium, Kaiser Aluminium, Hindalco Industries Ltd., Thyssenkrupp, AMG (Advanced Metallurgical Group), VSMPO-AVISMA Corporation, Aluminium Precision Products, Inc., Mifa Aluminium, Wuxi HENG TAI AEROSPACE Science and Technology Co., Ltd., and UACJ Corporation
Market Highlights
The global aerospace aluminium market is accounted for to register a CAGR of 7.2% during the forecast period and is estimated to reach USD 15152.77 million by 2032.
The global aerospace aluminum market is growing at a high rate, and the main driving force behind this trend is the increasing demand for lightweight materials. Lightweight materials are of prime importance in aerospace engineering as they directly impact fuel efficiency, performance, and sustainability. As the global aerospace industry continues to expand, lightweight materials, especially aluminum alloys, are becoming a cornerstone of aircraft design and manufacturing. This increasing focus on weight reduction is due to several key factors, which involve fuel cost reduction, environmental concern, technological advancement, and the need for higher performance in both commercial and military aerospace applications. A considerable influence of weight on the consumption of fuel has always been one of the key driving factors for the demand for lightweight materials in aerospace. Aircraft fuel costs are one of the largest areas of operational expense for commercial airlines. Every kilogram added to an aircraft increases the fuel consumed by that aircraft and increases the operational cost of that aircraft. Conversely, saving weight can save hundreds of thousands of dollars in fuel costs over the life of the aircraft. In order to reduce operation cost, airlines are incurring pressure on manufacturers for reduction of the weight of aluminum alloy that provides an optimal strength and weight balance. An example is the advanced substitution of traditional materials using aluminium alloys or composite material reducing the aircraft's overall weight, thus low consumption of fuel, lesser emission of carbon di oxide, and in total better efficiency. This makes lightweight aluminum a preferred choice for major aircraft manufacturers like Boeing and Airbus, which design their planes with a keen focus on fuel savings. Sustainability has become an increasingly important factor in the aerospace industry, driven by global concerns over climate change and environmental degradation. The aviation sector is one of the largest carbon-emitting industries. Manufacturers have a huge role to play in the production of more environment-friendly aircraft. Aluminum alloys and other lightweight materials help improve fuel efficiency and lower carbon emissions by reducing the weight of aircraft. Fuel savings from the use of aluminum translate into direct reductions in emissions per flight. In addition, aluminum is highly recyclable and has a lower environmental impact in its lifecycle compared to some other materials. This makes it a more sustainable option in the long term, aligning with the aerospace industry's sustainability goals. These advancements allow engineers to design lighter and stronger aircraft structures, which are essential for both commercial aviation and military aerospace applications. As for instance, the development of aluminium-lithium alloys helps create even lighter and efficient materials that contribute to lowering the aircraft weight while maintaining, if not improving, the strength and durability. Moreover, innovations in manufacturing processes such as additive manufacturing and advanced forging techniques further add the benefits from which aluminium alloys can be considered beneficially applicable in aerospace applications, since they can produce complex parts of lesser weight and optimized performance. The other important factor is the growing demand in air travel around the world. In the emerging economies, there is an increased call for lightweight materials. Most of the people in this world can now afford traveling by air. This will increase the demand for commercial aircraft, and subsequently, lead to the production of new aircrafts, which in turn increases the call for lightweight materials such as aluminum. This is further increased due to the rise of regional aircraft that are smaller, fuel-efficient, and designed for regional routes. These small aircraft focus on cost and fuel efficiency; therefore, they need materials that ensure safety and durability while decreasing weight.
Commercial aircraft is not the only field where lightweight materials are in high demand. Military and space applications also require them. Military aircraft and spacecraft must be lightweight to achieve better maneuverability, speed, and efficiency. For instance, stealth aircraft and drones use lightweight, durable materials for enhanced performance and operational range. Lightweight materials in the space sector reduce launch costs. Space agencies and private companies now increasingly use aluminum alloys for their satellite and spacecraft components with the aim of reducing their weight but still maintaining a strength and reliability under severe conditions. This has upped the demand for aerospace aluminum, especially in advanced projects of space exploration.
Growth in the global market for aerospace aluminum is primarily because of increased demand for lighter materials. Lightweight aluminum alloys have become significant factors due to substantial fuel savings as well as improved environmental and performance considerations for commercial as well as military applications. As the aerospace industry continues to innovate and expand, the focus on reducing weight without compromising strength or safety will remain a key priority, ensuring that aluminum alloys continue to play a central role in the design and manufacture of next-generation aircraft and spacecraft.
Access full report @ https://www.marketresearchfuture.com/reports/aerospace-aluminium-market-43292
Segment Analysis
The global aerospace aluminium market has been segmented based on Grade, Process, End Use, and Region.
The global aerospace aluminium Market segmentation, based on Grade has been segmented into segmented into 2024 Grade, 7075 Grade, 6061 Grade, 6082 Grade, and Others. Among these, the 7075 Grade of aerospace aluminium is projected to dominate the global aerospace aluminium market revenue through the projected period. 7075 grade aluminum is considered one of the strongest aluminum alloys available and is particularly favored in the aerospace sector for its exceptional mechanical properties. With zinc as its primary alloying element, 7075 offers high strength, low weight, and excellent resistance to stress corrosion cracking, making it ideal for highly stressed structural components such as aircraft frames, landing gears, and military applications. The alloy's ability to retain its strength at elevated temperatures adds to its appeal in aerospace applications where performance is critical. The processing techniques for 7075 have evolved, leading to improved fabrication methods and enhanced characteristics, ensuring that components manufactured from this alloy can withstand the rigorous demands of flight and combat environments.
In Process segment, the market is categorized into Casting, Extrusion, Welding, Forging, and Others. The Casting segment is dominant with the largest market share in the aerospace aluminium industry. Casting is a pivotal process in the global aerospace aluminum market, allowing for the production of intricate components with high dimensional accuracy and complex geometries. In this process, molten aluminum is poured into molds, where it solidifies into the desired shape. Various casting techniques, such as sand casting, die casting, and investment casting, cater to different manufacturing needs and specifications. Investment casting, for instance, is particularly valued in aerospace applications due to its ability to create parts with excellent surface finish and detail, making it ideal for critical components like engine housings, brackets, and structural elements. The casting process not only reduces material waste but also enables manufacturers to produce lightweight components that contribute to overall fuel efficiency in aircraft. As aerospace designs continue to evolve, advancements in casting technologies, including improved alloy formulations and process automation, enhance the capabilities and performance of cast aluminum parts, ensuring they meet the rigorous safety and performance standards required in the industry.
In End Use segment, the market is categorized into Commercial Aviation, Business & General Aviation, Military & Defense, and Others. The dominant market share in the aerospace aluminium industry is expected to be held by Commercial Aviation and the second dominant segment is Business & General Aviation. The commercial aviation segment is a major driver of the global aerospace aluminum market, as it encompasses a vast array of aircraft used for passenger and cargo transport. Airlines are continually seeking ways to improve fuel efficiency and reduce operational costs, and aluminum’s lightweight properties make it an ideal choice for airframe construction, wings, and other structural components. Modern commercial aircraft, such as the Boeing 787 and Airbus A350, utilize advanced aluminum alloys extensively to achieve optimal performance and fuel savings. Additionally, the trend towards larger, more fuel-efficient aircraft has increased the demand for high-strength, lightweight aluminum materials that can withstand the rigorous demands of flight while maintaining safety standards. The ongoing recovery of global air travel, combined with the introduction of new aircraft models and advancements in aluminum manufacturing technologies, positions the commercial aviation sector as a key area of growth within the aerospace aluminum market.
Regional Analysis
By Region, the aerospace aluminium market is segmented into North America, Europe, Asia-Pacific, Middle East & Africa, and Latin America. The North America aerospace aluminium market holds a considerable market share and is also forecasted to hold the largest share during the forecast period. The North American aerospace aluminum market holds a significant position in the overall aerospace industry, with strong growth being driven by increasing demand for lightweight, high-strength materials in aircraft manufacturing. Aluminum is predominantly used due to its high strength-to-weight ratio, resistance to corrosion, and cost-effectiveness. Aluminum is highly in demand in the region across commercial, military, and space applications. The U.S. is the biggest producer and consumer of aerospace aluminum, and the two companies, Boeing and Lockheed Martin, make up the highest percentage in terms of usage for aircraft and spacecraft parts made from aluminum. Alloys like 2024 and 7075 are more highly sought after for their added durability and resistance to stress and fatigue. The market is influenced by factors such as growth in air travel, military procurement, advancement in aerospace technology, and sustainability initiatives. Manufacturers are increasingly focusing on reducing carbon emissions, which has increased the demand for lightweight materials to improve fuel efficiency, further driving the demand for aerospace-grade aluminum.
Key Findings of the Study
-
The global aerospace aluminium market is expected to reach 15152.77 million by 2032, at a CAGR of 7.2% during the forecast period.
-
The North America region accounted for the fastest-growing global market.
-
Based on Grade, the 7075 Grade segment was attributed to holding the largest market in 2023.
-
Based on Process, the Casting segment was attributed to holding the largest market in 2023.
-
Based on End Use, the commercial aviation segment was attributed to holding the largest market in 2023.
-
Alcoa Corporation, Constellium, Kaiser Aluminium, Hindalco Industries Ltd., Thyssenkrupp, AMG (Advanced Metallurgical Group), VSMPO-AVISMA Corporation, Aluminium Precision Products, Inc., Mifa Aluminium, Wuxi HENG TAI AEROSPACE Science and Technology Co., Ltd., and UACJ Corporation are the key market players.
Leading companies partner with us for data-driven Insights
Kindly complete the form below to receive a free sample of this Report
Companies Covered | 15 |
Pages | 128 |
Certified Global Research Member
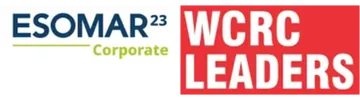
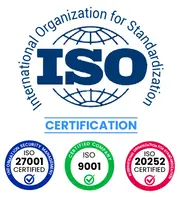
Why Choose Market Research Future?
- Vigorous research methodologies for specific market.
- Knowledge partners across the globe
- Large network of partner consultants.
- Ever-increasing/ Escalating data base with quarterly monitoring of various markets
- Trusted by fortune 500 companies/startups/ universities/organizations
- Large database of 5000+ markets reports.
- Effective and prompt pre- and post-sales support.
Tailored for You
- Dedicated Research on any specifics segment or region.
- Focused Research on specific players in the market.
- Custom Report based only on your requirements.
- Flexibility to add or subtract any chapter in the study.
- Historic data from 2014 and forecasts outlook till 2040.
- Flexibility of providing data/insights in formats (PDF, PPT, Excel).
- Provide cross segmentation in applicable scenario/markets.